Bungalow with 2010 Addition: Presents Benefits of the Home MVP Program and Building Upgrades
2,900 Square Foot – Winchester, MA
In our Bungalow with 2010 Addition we focus on our Winchester Example Project, the Homeowners’ primary goal was to eliminate use of fuel oil because of risk of adverse health effects. Their secondary goals were to improve comfort, reduce operating cost and reduce carbon emissions.
The Bungalow with 2010 Addition consists of two wings. There is an original 1937 Cape-style which was expanded to finish patio/deck areas decades prior to purchase by the current owners in 1993. An addition containing a master bedroom and master bath was added in the early 2000s.
Prior to Achieve’s work, the house was heated by a fuel oil boiler supplying baseboards in the original house and hydronic forced hot air in the addition. Air conditioning was installed in the addition but not in the remainder of the house. Domestic hot water was supplied by an indirect/sidearm tank connected to the boiler. The house is on a steep hill with abundant bedrock outcroppings. Fuel oil use was very high with over 2,000 gallons being consumed each year.
Design & Installation for Bungalow with 2010 Addition:
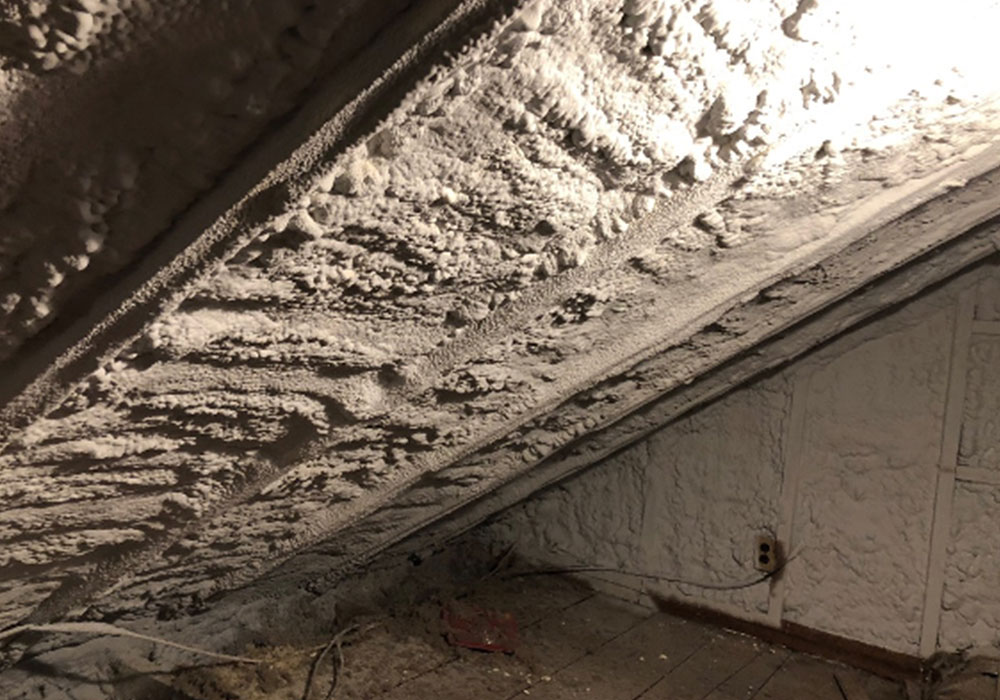
Spray Foam Insulation Completed as Part of Home Energy MVP Program
Manual J:
Once we had useful information regarding the building envelope, we evaluated the heating and cooling loads of the home using software that provides a Manual J result. There is not a connection possible for ducting between the Original House and Addition so a decision was made to provide two GSHPs supplying three heating/cooling zones.
Ground Source Design:
Achieve recommended a vertical, closed-loop, ground heat exchanger (VCL). The design of the VCL consisted of two borings using 1.25” ID HDPE piping. Each boring was designed to be drilled to a depth of 380 feet. As is our practice, we specified high thermal conductivity graphite-bentonite grout material to improve heat transfer.
Equipment Selection:
For the Bungalow with 2010 Addition, the Homeowner was interested in the greatest possible efficiency. As such, Achieve selected a WaterFurnace 7 Series GSHP (variable-capacity compressor and fan) for the main house and a smaller 5 Series Indoor Split (Dual-speed compressor and variable-speed fan) for the Addition. Both GSHPs were specified with variable-speed loop pumping to increase efficiency.
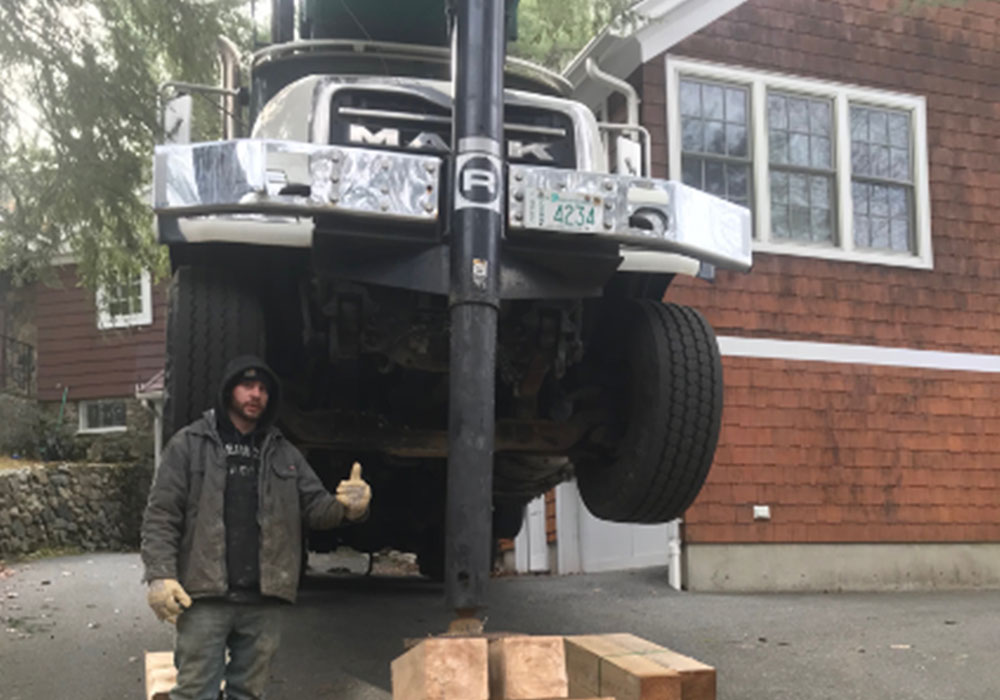
Special Challenges:
- The Bungalow with 2010 Addition Project is on a steeply sloped lot with bedrock outcroppings. This resulted in very limited options for placement of the VCL. It was necessary to support the drilling rig on timber cribbing – no small task for an 80,000 pound machine (see Photo 3).
- The steep slopes and relatively small lot also complicated management of drilling water. To avoid discharge to the street (and in accordance with discussion Achieve had with the Conservation Commission) drilling fluid was managed in a settling tank.
- Since the construction of the Addition allowed for no piping to route from the Original House, the VCL was connected to each GSHP separately via a piping excavation.
- Ducting had a high degree of difficulty. To reach all areas of the Original House had to be routed through and around crawl spaces to reach all areas of the first floor.
Financial Incentives:
Home Energy MVP Program:
The Home Energy MVP Program contributed substantially to the use of GSHP, insulation upgrades and the heat pump water heater. The contractor-facing incentive for the project is more than $20,000. This award is based upon fuel switching and efficiency upgrades. The incentive substantially offset key portions of this project that might not have been feasible for an Installer that is not part of the Home Energy MVP (closed pilot program)
MassCEC:
The project qualified for what was a higher level of grant available in early 2018. The grant award was $17,500.
Alternative Portfolio Standard:
The project qualifies for Alternative Energy Credits. As with most residential installations, 10-years of credits were provided at one time via ‘pre-minting’. The AECs will be transacted once minted with an estimated value of approximately $8,000.
Federal Tax Credit:
The project is eligible for a 30% Federal Tax Credit on the entire GSHP installation exclusive of distribution system (ducting). The value of this incentive is over $20,000.
Results for Bungalow with 2010 Addition:
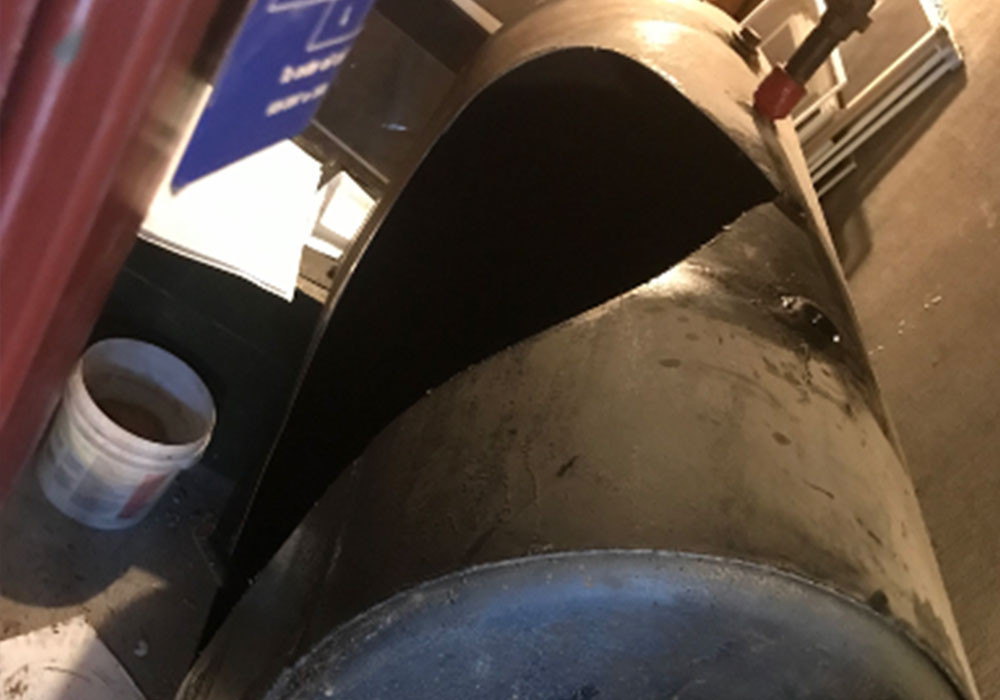
Photo 4: Fuel Oil Tank Removal
- Per the Homeowner’s primary goal for the Bungalow with 2010 Addition, fuel oil use and storage at the home has been eliminated.
- The Homeowners report a dramatic improvement in comfort, especially on cold days. This is a result of both the GSHP installation and the insulation upgrades.
- The Homeowners have noticed a dramatic reduction in icicles and ice dams. This is a result of the spray foam insulation that encapsulated the attic rafters, and is despite a higher heating setpoint (72F v. 68F). The following photos show ice dams in 2013 and an almost complete lack of icicles in 2018/2019. This furthers energy efficiency because the Homeowners no longer have to use heating wires to abate the ice dams.
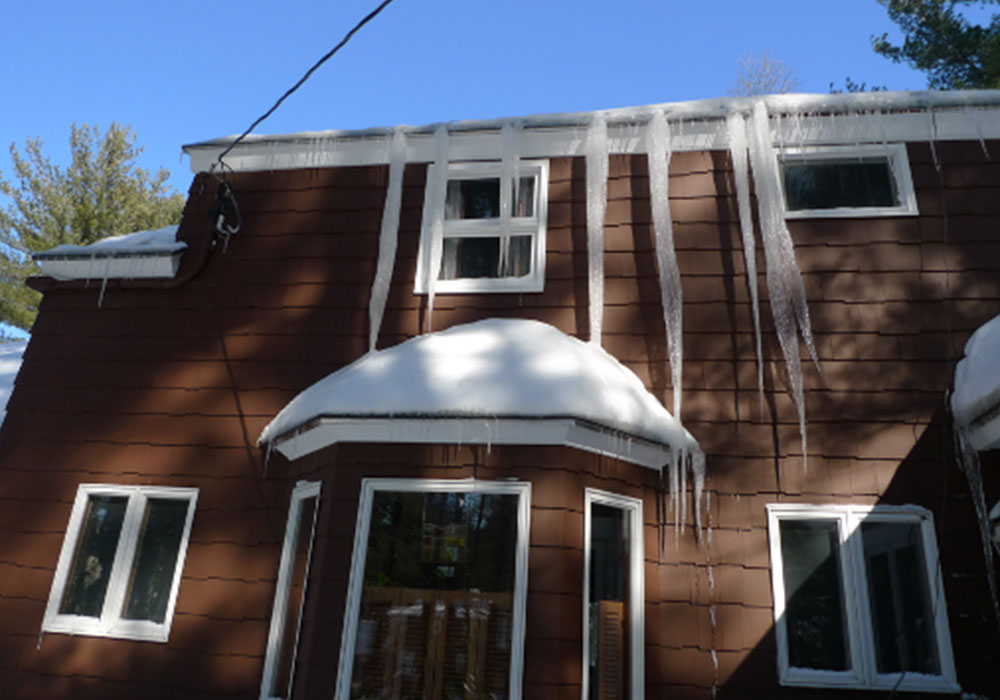
Icicles/Ice Dams Prior to Insulation Upgrades
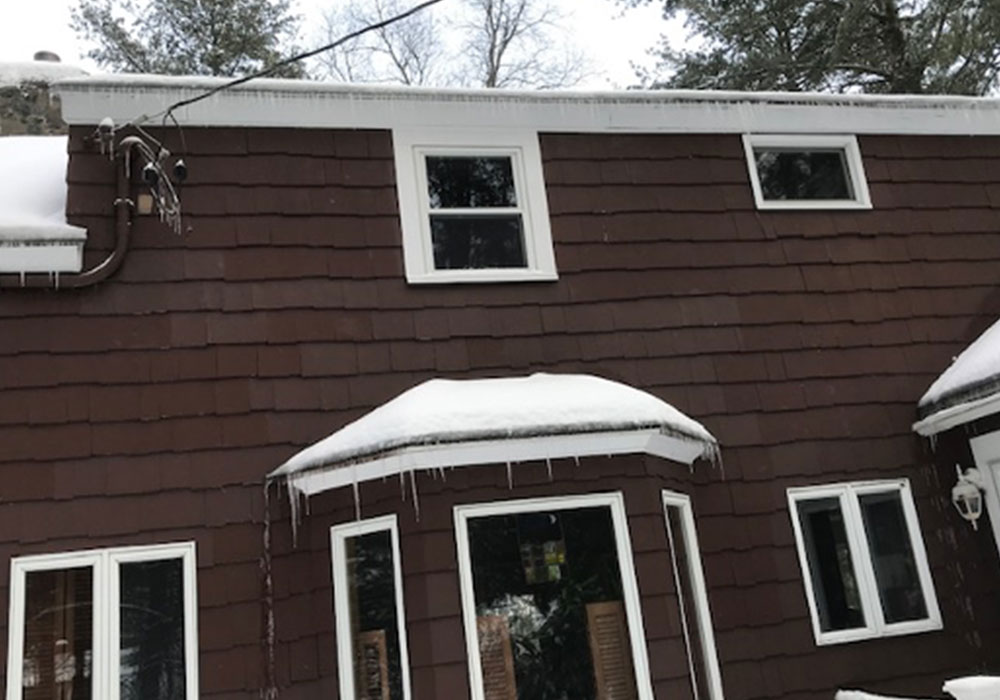
Ice Issue Mitigated by Insulation/GSHP Install
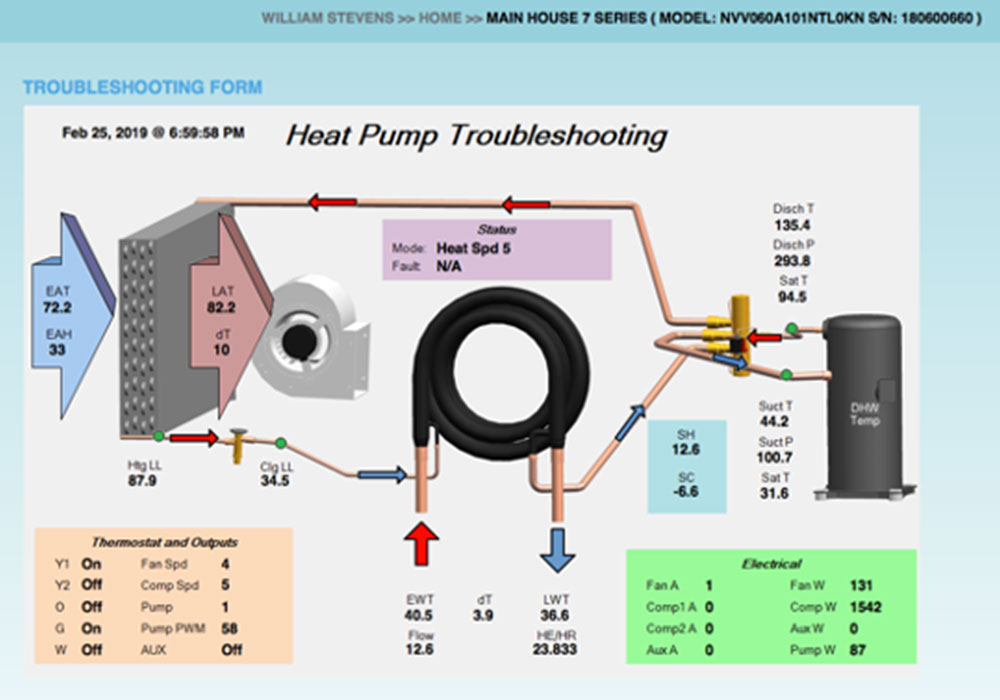
- The Homeowners note that the GSHP system is much quieter than their old heating system. This is because noisy combustion has been eliminated and because of the variable-speed fans within the GSHPs.
- Homeowners report operating cost is noticeably lower than with the former fossil-fuel system. This is despite a higher heating setpoint (72F v. 68F).
- Remote access and monitoring is included in the system price with no on-going subscription fees. Figure 1 shows some of the data that is available every 10-seconds.
Conclusion Regarding Project Approach:
Without Achieve’s whole-house approach, the GSHP installation would have faced a much higher heating load. As such, a larger, more expensive system would have been required. Given drilling limitations, it may not have been possible to complete the installation. We believe this project represents a significant evolution for GSHP Installations bringing retro-fit performance much closer to that of new construction.
How can we help with your project?
Whether you are installing a system for a new construction or replacing an older system, our experienced team of dedicated professionals is here to answer all questions and ensure you are making the right choices. We believe EVERY client deserves 100% of our time and attention. Please contact us to see how we can be of service to you.