Historic Mill: Presents Conversion of an 1880’s Mill to Sustainable Office Space
Arlington, MA
The owners were renovating an historic mill in Arlington, Massachusetts. The first floor was vacant and a tech company occupied the second floor. The Mill was c. 1880 heavy timber and brick structure. The conversion goal was a bright and inviting Class A office space on the first floor with multiple private offices and open work areas for a co-working organization. Maintaining a short schedule to meet the requirements was a key to project success. The historic brick and timber construction was left exposed removing the potential of providing insulation.
The historic mill building was heated via a fuel oil-fired steam system. HVAC upgrade options were:
1.) Natural gas furnaces and traditional air conditioners or
2.) Ground source heat pump (GSHP).
The Owner first favored a natural gas system based on cost and anticipated installation time. During planning, the gas main was found to be within Massachusetts Avenue approximately 200 feet from the building. The cost of installing the natural gas line was approximately $30,000. More importantly, the Utility would not promise a schedule for the gas line installation. The potential long delay threatened loss of the business as a tenant.
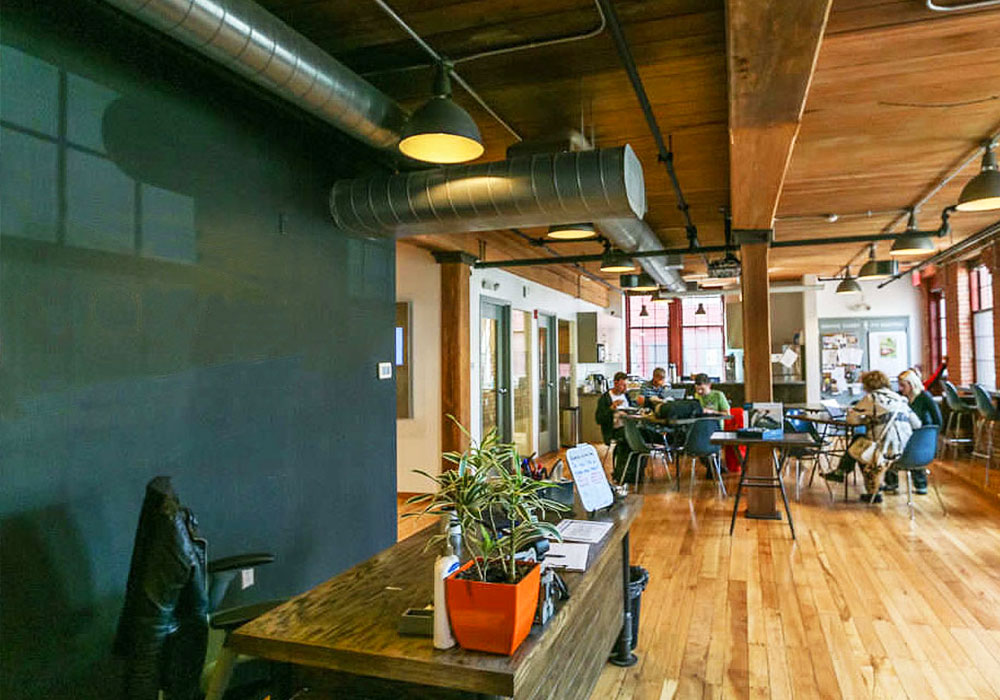
View of the completed WorkBar facility.
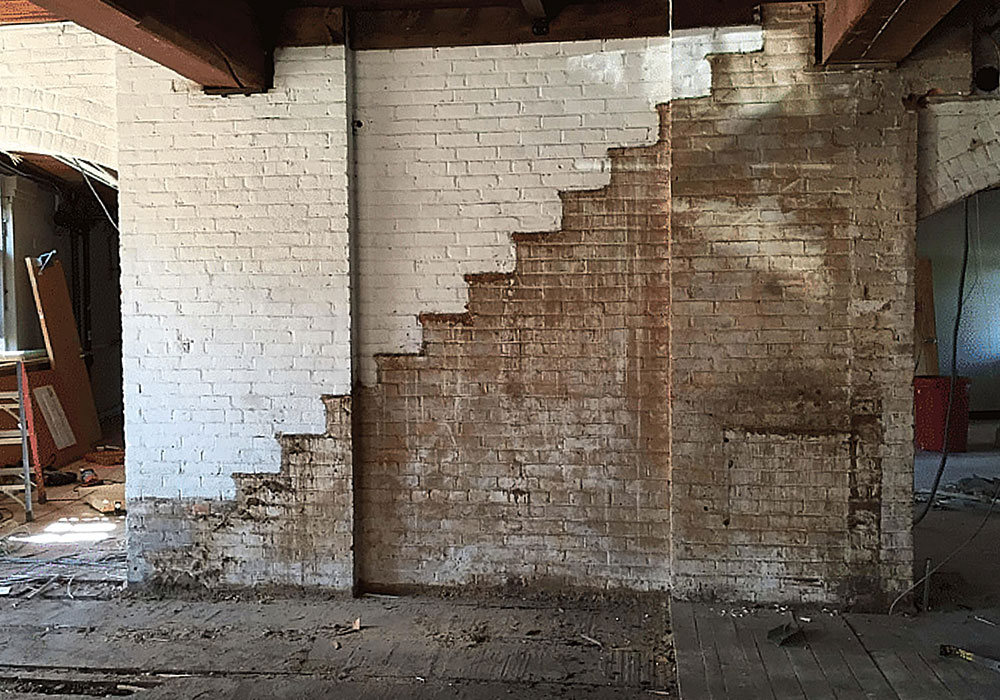
Rough space prior to construction.
The Results:
There were permitting challenges for the project: There were permitting challenges for the project: the project was within a wetland resource area; the available space for the ground source required crossing Mill Brook and a large sewer main. Achieve devised a method for pipe routing and obtained the required special permits.
The ground source consisted of eight vertical bores drilled in native Diorite and Gabbro. Each boring was completed with a 1.25” ID HDPE u-bend and backfilled with graphite-enhanced grout with a thermal conductivity of 1.6 Btu/hr-ft-°F. The borings were plumbed in parallel in pairs and combined in a pipe vault. From the vault, 4” ID piping traversed the sewer main and Brook.
Achieve installed variable-speed central loop circulation that supported six WaterFurnace GSHPs. Three of the GSHPs utilize variable-speed compressors and condition up to six zones each. The other three GSHPs utilize two-stage compressors and support up to four zones each. The first floor design alone had 15 zones. The building has 24 zones. Each GSHP is monitored remotely using a WaterFurnace Aurora Web-Link (AWL).
Construction was completed on time and the renovated facility opened to great fanfare. Based upon data from the AWLs, for the 12-months from March 2017 thru February 2018, the approximately 12,000 sq. ft. historic building had total heating and cooling cost of $6,415 at $0.18/kWh. Of this, about $1,500 was cooling of a server room.
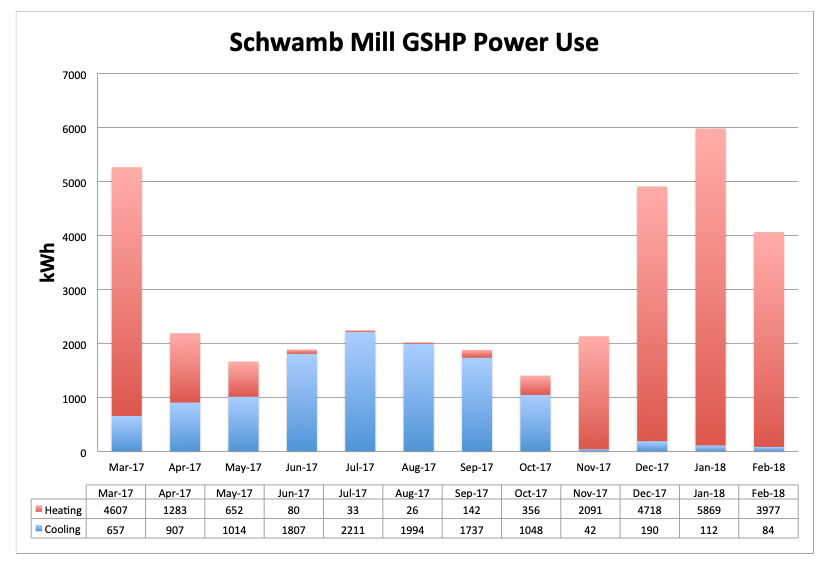
The Owner has told Achieve that this is the lowest maintenance, quietest, and lowest operating cost heating system at any of their numerous facilities. Since this case study was developed, the GSHP system has been expanded as this co-workspace has expanded to occupy the entire building. The system now also supports an unrelated tenant in the adjacent mill building.